Planar Constraint

Lovely.

The table holds the pins. the pins are located at a, b, and c.
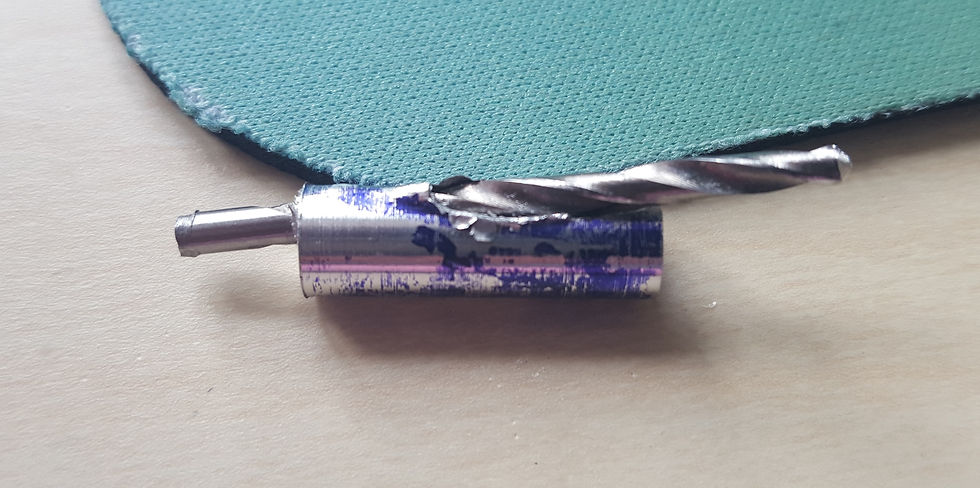
If your first center drill breaks, make sure you go in again with a second.... or else...

Lovely.
Planar Constraint
2016
I built the constraint out of ABS plastic and aluminum I scavenged from the MIT MakerWorks. I milled the slots and holes and lathed the cylinder pieces. The design turned out to work great and the ABS was very low friction which meant accurate results.
When we tested the design, the results correlated exactly with the model. I could constrain the planar object with three pins if the force was applied at the center of the block. Applying the force at the sides, however, resulted in an inexact constraint unless the forces were applied in very certain positions. Using four pins led to an exact constraint from all external forces.
All in all, the assignment was very cool. I'm starting to get a knack for how the positions of constraints allows for positioning and resistance towards forces and moments. This will be a cool toy I can keep on my desk for the future.
In this assignment, I tried to constrain a 2D planar object using only single points of contact. I developed a design for the constraints using slots in which pins were placed to constrain the square block. I used the equations of force and moment to develop a model of the system. Then I analyzed the model in MatLab to see where I should put the constraints.
After modeling in MatLab, I checked my numbers and met with my peers to discuss the design. We thought the design was good and allowed for maximum flexibility. We had some doubts whether three pins could totally constrain the block when a force was applied at varying angles to the center of the block. The best way to check was to build the thing.
The video below is a quick 7 minute summary of the design, analysis, build, and testing of my planar constraint. Be sure to have your sound on.
For the images above, click on them to open up a bigger version and follow a link to a pdf you can zoom in on.